This article provides a detailed overview of the key processes and considerations in electroplating, chemical plating, and hot air leveling for Flexible Printed Circuits (FPC). It highlights the importance of pre-treatment in electroplating for maintaining FPC performance, the challenges in controlling plating thickness, and issues related to post-plating stains. Additionally, the article discusses the application of chemical plating when FPC conductors cannot serve as electrodes and the quality concerns that may arise. Finally, it examines the use of hot air leveling on FPCs, focusing on adhesion strength and moisture resistance. Through this article, readers will gain a deeper understanding of the common challenges in FPC manufacturing and their solutions.From the demand side, flexible circuits More in line with the psychological expectations of consumers, willing to pay for the things they like. https://gekunflex.com/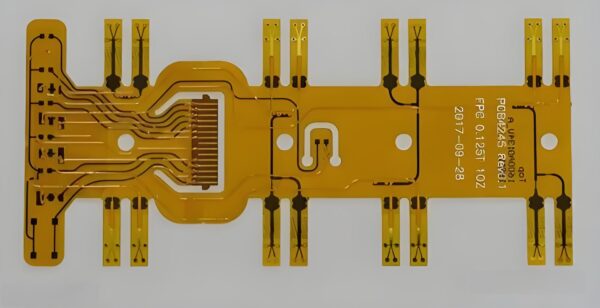
FPC manufacturer
FPC manufacturer
FPC Plating Process
1. Pre-treatment for FPC Electroplating
After the flexible printed circuit (FPC) undergoes the coating process, the exposed copper conductors may be contaminated by adhesives or ink. Additionally, oxidation and discoloration caused by high-temperature processes can occur. To ensure good adhesion of the plating, these contaminants and oxidation layers must be removed, leaving the conductor surface clean.
However, some contaminants are strongly bonded to the copper conductor, making it difficult to remove them with weak cleaning agents. Strong alkaline abrasives and brushing are typically used for this treatment. Since the adhesive used in the cover layer is often epoxy-based, which is not resistant to alkaline agents, this can weaken bonding strength. Although not immediately apparent, during the electroplating process, the plating solution may seep into the edges of the cover layer, and in severe cases, cause delamination of the cover layer.
At the final soldering stage, solder might seep beneath the cover layer. Therefore, the pre-treatment cleaning process has a significant impact on the basic characteristics of the FPC, making it essential to pay close attention to the processing conditions.
2. Thickness of FPC Electroplating
The deposition rate of electroplating metal is directly related to the intensity of the electric field, which varies depending on the shape of the circuit and the position of the electrodes. Generally, the thinner the conductor line and the sharper the terminal end, the stronger the electric field, leading to a thicker plating in those areas.
In FPC applications, there are often wide differences in the width of conductor lines within the same circuit, resulting in uneven plating thickness. To prevent this, auxiliary cathode patterns are added around the circuit to absorb uneven current distribution across the plating pattern, ensuring uniform plating thickness across all areas.
Electrode structure is key here. A compromise approach can be adopted, where stricter standards apply to areas requiring high plating uniformity, such as molten solder (lead-tin) and gold plating for metal wire bonding, while areas requiring plating for general corrosion protection may have more relaxed thickness requirements.
FPC manufacturer
3. Contamination of FPC Electroplating
Immediately after electroplating, the plated surface may appear fine, but stains, dirt, or discoloration can appear over time. Often, these issues are not detected during factory inspections but are discovered during customer acceptance tests. This happens when the plated surface is not adequately rinsed, leaving residual plating solution, which reacts chemically over time, especially on the flexible surface due to its softness and uneven texture.
To prevent this, thorough rinsing and drying are essential. A high-temperature thermal aging test can verify whether rinsing was sufficient.
FPC Chemical Plating
When the conductor to be plated is isolated and cannot serve as an electrode, chemical plating must be used. Chemical plating solutions are highly reactive, and a common example is chemical gold plating. The chemical gold plating solution is an alkaline solution with a very high pH value.
When using this process, it is easy for the plating solution to seep beneath the cover layer, especially if the lamination quality control is poor, leading to weak adhesion. Displacement reactions in chemical plating exacerbate this problem, making it difficult to achieve ideal plating conditions.
FPC Hot Air Leveling (HASL)
Hot air leveling was originally developed for rigid printed circuit boards (PCBs) to coat them with lead-tin. However, this technique has been applied to FPCs due to its simplicity. Hot air leveling involves immersing the board vertically into molten lead-tin and blowing off excess solder with hot air.
These conditions are quite harsh for FPCs. Without special measures, FPCs cannot be immersed in molten solder. To address this, FPCs must be clamped between titanium-steel meshes before immersion. Additionally, the surface of the FPC must be cleaned and coated with flux beforehand.
Due to the harsh nature of the hot air leveling process, solder may seep beneath the edges of the cover layer, especially if the bonding strength between the cover layer and the copper foil is weak. Since polyimide films are prone to moisture absorption, moisture can evaporate suddenly under the heat, causing blistering or even delamination of the cover layer. Therefore, drying and moisture control must be performed before FPC hot air leveling.
FPC manufacturer
FPC manufacturer
Gekun is a leading manufacturer specializing in high-quality Flexible Printed Circuits (FPC). With years of experience in the industry, Gekun provides advanced FPC solutions tailored to various industries, including telecommunications, medical devices, automotive, and consumer electronics. Their manufacturing process emphasizes precision, reliability, and innovation, ensuring excellent performance and durability. For businesses looking for custom FPC designs or mass production, Gekun stands out as a trusted partner, offering both competitive pricing and cutting-edge technology.
For more information on Gekun¨s FPC manufacturing capabilities, you can visit their official website or contact their team for specific inquiries.