Cold heading (extrusion) technology is a main processing technology in fastener forming process. Cold heading (extrusion) belongs to the field of metal pressure processing. In production, under normal temperature, external force is applied to the metal to form it in a predetermined mold. This method is usually called cold heading.The above conclusions show that Fastener To a great extent, it can bring new vitality to the market and make the industry develop well. https://www.chinatianlong.com/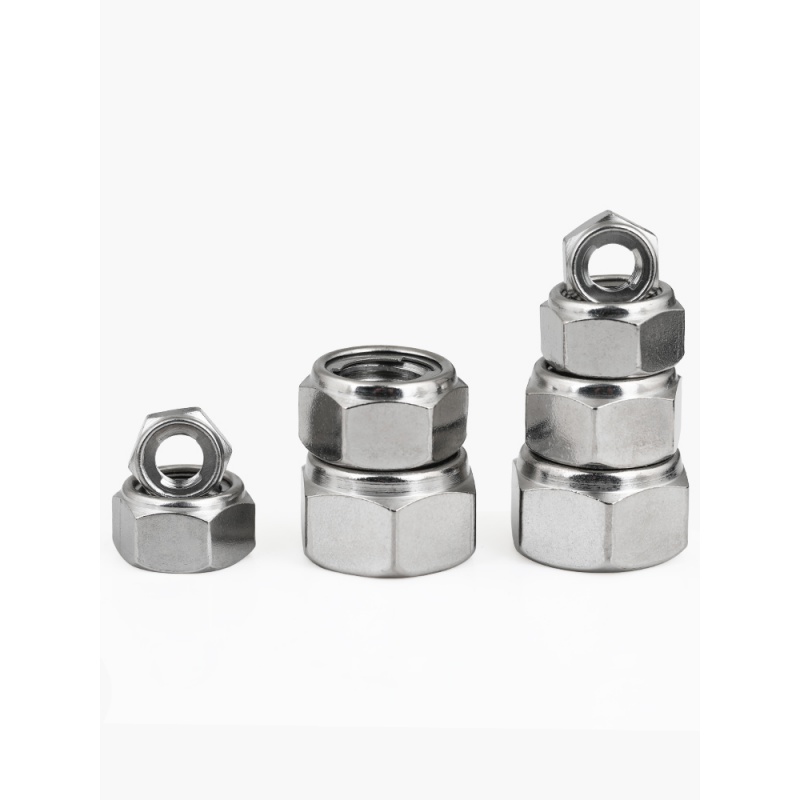
In fact, the forming of any fastener can not only be achieved by cold heading, but also accompanied by various deformation methods such as forward and backward extrusion, compound extrusion, punching and rolling in the process of cold heading.
Therefore, the name of cold heading in production is just a habitual name, more precisely, it should be called cold heading (extrusion).
Cold heading (extrusion) method is a kind of processing method with high comprehensive economic benefit, which is widely used in the fastener industry and is also an advanced processing method widely used at home and abroad.
Therefore, how to make full use of and improve the plasticity of metal, master the mechanism of plastic deformation of metal, and develop a scientific and reasonable cold heading (extrusion) processing technology for fasteners is the purpose and purpose of this paper.
First, the basic concept of metal deformation
Deformation refers to the sum of the relative displacements of the tiny particles that make up the metal when it is stressed (external force and internal force) under the condition of maintaining its integrity.
1 Types of deformation
A. elastic deformation
The ability of a metal to recover its original shape and size when the external force is removed is called elastic deformation.
The quality of elasticity is measured by elastic limit and proportional limit.
B. Plastic deformation
Under the action of external force, a metal is permanently deformed (refers to the deformation that cannot be restored to its original state after removing external force), but the integrity of the metal itself will not be destroyed, which is called plastic deformation.
The plasticity is expressed by elongation, area shrinkage and yield limit.
2 evaluation method of plasticity
The plasticity is expressed by elongation, area shrinkage and yield limit.
In order to evaluate the plasticity of metals, a numerical index, called plasticity index, is often used.
The plasticity index is expressed by the plastic deformation at the moment when the steel sample begins to fail. In production practice, the following methods are usually used:
(1) Tensile test
The tensile test is expressed by elongation δ and area shrinkage ψ. It indicates the plastic deformation ability of steel samples under uniaxial tension, which is a common plastic index in metal material standards. The values of δ and ψ are determined by the following formula:
Where: L0, lk-the length of the original gauge of the tensile specimen and the gauge after failure.
F0, Fk!! the cross-sectional area of the original and broken parts of the tensile specimen.
(2) Upsetting test is also called flattening test.
It is to make the sample into a cylindrical shape with the height Ho 1.5 times of the original diameter Do of the sample, and then flatten it on a press until the first visible crack appears on the surface of the sample. At this time, the compression degree εc is the plastic index. Its value can be calculated by pressing the following formula:
Where Ho!! is the original height of the cylindrical sample. Hk!! the height of the sample when the first visible crack appears on the side surface during flattening.
The torsion test is expressed by the torsion angle or the number of torsion turns when the sample is twisted on the twisting machine. Tensile test and upsetting test are commonly used in production.
No matter which test method, it is relative to a specific stress state and deformation condition.
The plasticity index obtained from this is only a relative comparison, which only shows the plasticity of a certain metal under what deformation conditions.
3 Main factors affecting metal plasticity and deformation resistance
The concept of metal plasticity and deformation resistance: metal plasticity can be understood as the ability of metal to change its shape stably without destroying the connection between particles under the action of external force. And the force that the metal reacts to the tool and die when it is deformed is called deformation resistance.
The main factors affecting metal plasticity and deformation resistance include the following aspects:
A. Influence of metal structure and chemical composition on plasticity and deformation resistance
The metal structure depends on the chemical composition of the metal, the lattice type of its main elements, and the nature, quantity and distribution of impurities. The fewer constituent elements, the better the plasticity.
For example, pure iron has high plasticity.
Carbon in iron is a solid melt and has good plasticity, while it is a compound, so its plasticity decreases.
For example, the compound Fe3C is actually very brittle. Generally, the increase of other elements in steel will also reduce the plasticity of steel.
With the increase of carbon content in steel, the resistance indexes (бb, бp, бs, etc.) of steel all increase, while the plasticity indexes (ε, ψ, etc.) all decrease. When the carbon content in steel is increased by 0.1% during cold deformation, its strength limit бs is increased by about 6 ~ 8 kg/mm2.
Sulfur exists in steel as iron sulfide and manganese sulfide. Iron sulfide is brittle, and manganese sulfide is elongated in the process of pressure processing, thus reducing the mechanical index in the transverse direction perpendicular to the fiber. So sulfur is a harmful impurity in steel, and the less the content, the better.
Phosphorus in steel improves deformation resistance and reduces plasticity. Steel with phosphorus content higher than 0.1% ~ 0.2% has cold brittleness. Generally, the phosphorus content of steel is controlled at 0.00%. The distribution of other impurities such as low melting point in metal matrix has great influence on plasticity.
In a word, the more complex the chemical composition in steel is, the more the content is, and the greater the influence on the resistance and plasticity of steel is. This explains why some high alloy steels are difficult to be cold heading (pressing).
B. Effect of deformation speed on plasticity and deformation resistance
Deformation velocity is the relative displacement volume per unit time:
The deformation speed should not be confused with the movement speed of the deformation tool, but should also be conceptually distinguished from the movement speed of particles in the deformation body.
Generally speaking, with the increase of deformation speed, deformation resistance increases and plasticity decreases.
In cold deformation, the influence of deformation speed is not as significant as that in hot deformation, which is due to the absence of hardening elimination process.
However, when the deformation speed is particularly high, the heat generated by plastic deformation (that is, thermal effect) must not be separated. Increasing the temperature itself will improve plasticity and reduce deformation resistance.
C. the influence of stress state on plasticity and deformation resistance
Under the action of external force, internal force is generated in the metal, and its strength per unit area is called stress. The stressed metal is under stress.
A tiny elementary cube is separated from the deformed body, and the stress with unknown magnitude but known direction acts on the cube. This diagram representing the number and symbol of principal stresses at points is called principal stress diagram.
There are nine principal stress diagrams representing the stress state of metals, four of which are three-way principal stress diagrams, three are plane principal stress diagrams and two are unidirectional principal stress diagrams, as shown in Figure 36-1.
Principal stress caused by tensile stress is positive sign, and principal stress caused by compressive stress is negative sign.
In metal pressure machining, the three-dimensional principal stress diagrams with the same sign and different sign are often encountered. Among the three-dimensional principal stress diagrams with different signs, the principal stress diagram with two compressive stresses and one tensile stress is the most common.
In the triaxial stress diagram with the same sign, when the compressive stresses in all directions are equal (б1=б2=б3), and there are no porosity and other defects in the metal, theoretically, plastic deformation cannot occur, only elastic deformation occurs.
Unequal triaxial compressive stress diagrams include deformation processes such as volume die forging, upsetting, closed punching, positive and negative extrusion, plate and profile rolling, etc.
In the actual production, the triaxial tensile stress diagram is rarely encountered. Only in the tensile test, when necking occurs, the stress line at the necking is the principal stress diagram of triaxial tensile, as shown in Figure 36-2.
During upsetting, due to the action of friction, it also presents a three-dimensional compressive stress diagram, as shown in Figure 36-3.
In a word, in the stress state of stressed metal, compressive stress is beneficial to the increase of plasticity, while tensile stress will reduce the plasticity of metal.
During upsetting, due to the action of friction, it also presents a three-dimensional compressive stress diagram, as shown in Figure 36-3.
In a word, in the stress state of stressed metal, compressive stress is beneficial to the increase of plasticity, while tensile stress will reduce the plasticity of metal.
D. influence of cold deformation hardening on metal plasticity and deformation resistance
The mechanical properties, physical properties and chemical properties of metals are changed after cold plastic deformation.
With the increase of deformation degree, all strength indexes (elastic limit, proportional limit, flow limit and strength limit) are improved, and the hardness is also improved. Plastic indexes (elongation, area shrinkage and impact toughness) are decreased; Resistance increases; Corrosion resistance and thermal conductivity are reduced, and the magnetic properties of metals are changed. In plastic deformation, the sum of these properties changes of metals is called cold deformation hardening, or hardening for short.
E. the influence of additional stress and residual stress
In deformed metal, the stress distribution is uneven, and it is hoped to obtain larger deformation where the stress distribution is more, and smaller deformation where the stress distribution is less.
Because of the integrity of the deformed metal itself, there are internal forces that are balanced with each other, that is, the so-called additional stress. When the deformation is terminated, these mutually balanced stresses exist in the deformed body, which constitutes residual stress and affects the plasticity and deformation resistance of the deformed metal in the later deformation process.