Touch sensors are integral to modern technology, enabling intuitive interactions with devices ranging from smartphones to industrial machinery. Understanding the science behind these sensors and addressing common performance issues can help optimize their functionality and ensure a seamless user experience. Here’s an in-depth look at how touch sensors work, their key features, and solutions to typical problems.Therefore, we should understand silicone rubber keyboard Many benefits, absorb and summarize, and use them. https://singway-touch.com/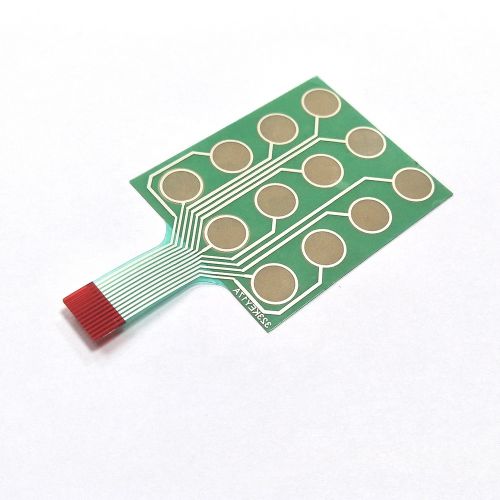
1. The Basics of Touch Sensors
Touch sensors operate by detecting and responding to touch input, converting physical interactions into electronic signals. The most common types include:
Capacitive Touch Sensors: Utilize the change in capacitance when a finger touches the screen. These sensors are highly sensitive and support multi-touch input.
Resistive Touch Sensors: Comprise two conductive layers separated by a small gap. Pressure on the screen causes the layers to touch, registering the input.
Infrared Touch Sensors: Use infrared light beams to detect touch by interrupting the light paths. These are effective for large displays and work in various lighting conditions.
Surface Acoustic Wave (SAW) Sensors: Employ ultrasonic waves to detect touch interactions. They provide high clarity and precision, ideal for high-resolution displays.
2. Key Features of Touch Sensors
Sensitivity: Determines how responsive the sensor is to touch input. High sensitivity sensors can detect even the lightest touches.
Accuracy: Measures how precisely the sensor can detect the location of touch. Higher accuracy is crucial for applications requiring fine detail, such as graphic design or data entry.
Durability: Refers to the sensor’s ability to withstand wear and tear, including exposure to contaminants, temperature fluctuations, and physical impact.
Multi-Touch Capability: Allows the sensor to detect multiple points of contact simultaneously, supporting gestures like pinching and swiping.
Response Time: The speed at which the sensor registers and responds to touch input. Faster response times enhance user experience by reducing lag.
3. Common Performance Problems and Solutions
Problem 1: Unresponsive Touch
Causes:
Dirty or Damaged Surface: Dirt, grime, or scratches can impede touch detection.
Calibration Issues: Sensors may need recalibration to function correctly.
Solutions:
Clean the Surface: Regularly clean the touch sensor with a soft, lint-free cloth. For stubborn residues, use a mild cleaning solution.
Recalibrate the Sensor: Follow the manufacturer¨s instructions to recalibrate the touch sensor for optimal performance.
Problem 2: Erratic Touch Response
Causes:
Electromagnetic Interference (EMI): Nearby electronic devices can interfere with sensor performance.
Inconsistent Pressure: Irregular or excessive pressure can cause erratic behavior.
Solutions:
Minimize EMI: Ensure that the sensor is shielded from potential sources of electromagnetic interference. Use appropriate grounding techniques to reduce EMI effects.
Ensure Consistent Pressure: Educate users on applying consistent pressure and avoid excessive force on the touch sensor.
Problem 3: Poor Sensitivity
Causes:
Environmental Conditions: Extreme temperatures or humidity can affect sensor performance.
Aging Sensor: Over time, touch sensors can lose their sensitivity due to wear and tear.
Solutions:
Maintain Optimal Conditions: Operate the sensor within the recommended temperature and humidity ranges. If necessary, use environmental controls to maintain these conditions.
Replace the Sensor: If sensitivity issues persist and the sensor is aging, consider replacing it with a new one.
Problem 4: Ghost Touches
Causes:
Electrical Noise: Interference from electrical noise can cause false touches.
Software Glitches: Bugs or glitches in the touch sensor¨s firmware can lead to ghost touches.
Solutions:
Reduce Electrical Noise: Use shielding and grounding techniques to minimize electrical noise. Ensure proper installation and maintenance of the sensor.
Update Firmware: Regularly update the sensor¨s firmware to address software bugs and improve performance.
Problem 5: Inaccurate Touch Location
Causes:
Misalignment: The touch sensor might not be properly aligned with the display.
Calibration Issues: Incorrect calibration can lead to inaccurate touch location detection.
Solutions:
Check Alignment: Ensure the sensor is correctly aligned with the display and adjust as needed.
Recalibrate: Perform a recalibration to correct any inaccuracies in touch location detection.